The TAILTEST research program comprises some critical research activities, which primarily involve:
- Development of a Test Rig for the certification of a rotorcraft tail,
- Experimental investigation of the mechanical behaviour of materials and building blocks for the V-tail,
- Validation of numerical simulations regarding the proposed materials in coupon and structural detail level,
- Development of methodologies for the detailed simulation of a full-scale V-tail
- Tailtest is a Clean Sky 2 project, related to the activities of the Clean Sky 2 project Light Innovative Flying Tiltrotor Tail LIFT
a) Experimental testing
The materials that are used for the manufacturing of the V-Tail’s components are tested in varying loading conditions, to establish the mechanical response of the building blocks. Experimental testing procedures include:
- Unnotched Tension
- Unnotched Compression
- Open Hole Tension
- Open Hole Compression
- Compression After Impact
- Interlaminar Fracture Toughness
- In-Plane Shear
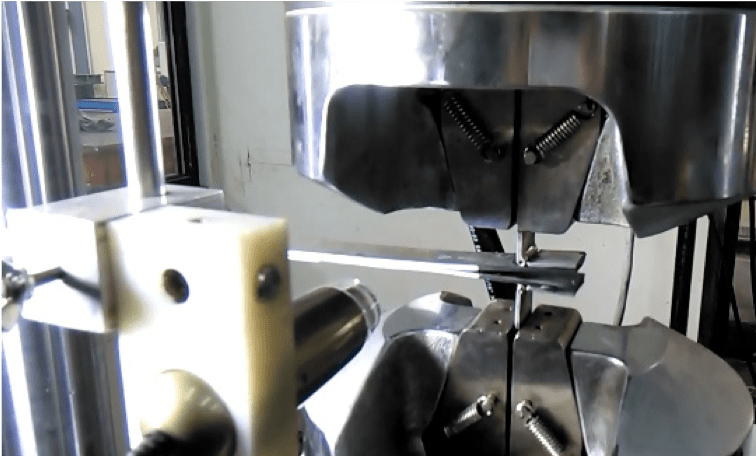
These tests can fully capture the mechanical response of the candidate materials.
Tests on panels at structural detail level will also be performed.
b) Test Rig Development
c) Model validation
Development of debonding model, numerical analysis and virtual testing will be primary and not just supportive tools for the realization of TAILTEST.
Five main simulation tasks will be performed:
- Development of damage / failure models for the joints for static and dynamic* loads
- Modelling of a spar-to-skin joint for validation and assessment purposes
- Numerical design and optimization of the optimum fuselage/fin joint
- Detailed FE analysis of the fin/fuselage structure to determine the boundary conditions between the two parts
- Numerical design and optimization of the test-rig
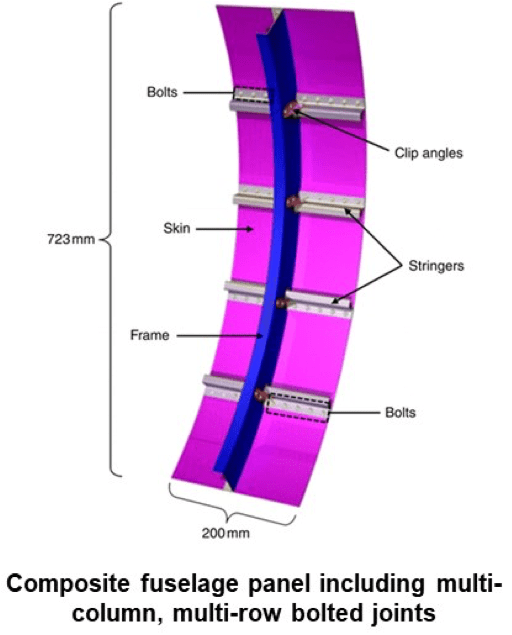
